top of page
WELCOME TO MY RESEARCH WEBSITE
DR. MOHAMAD REZI ABDUL HAMID
References:
1. D. S. Sholl and R. P. Lively, Nature, 532, 435, 2016
2. A.R. Smith and J. Klosek, Fuel Process. Technol., 70, 115, 2001
3. R. Faiz and K. Li, Desalination, 287, 82, 2012
4. N.W. Ockwig and T. M. Nenoff, Chem. Rev., 107, 4078, 2007
5. A. B. Hinchliffe and K. E. Porter, Chem. Eng. Res. Des., 78, 255, 2000
6. R. B. Eldridge, Ind. Eng. Chem. Res., 32, 2208, 1993
7. W. Ho and K. Sirkar, Membrane handbook, Springer Sci. & Business Media, 2012
8. M.T. Ravanchi, T. Kaghazchi and A. Kargari, Desalination, 235, 199, 2009
9. G.W. Meindersma and M. Kuczynski, J. Membr. Sci., 113, 285, 1996
Development of more energy efficient chemical separations, if applied to chemical, petrochemical & paper manufacturing alone, could save up to $4 billion of energy cost & decrease CO2 emission by 100 million tonnes per year. Thermally-driven distillation is one of the most widely used separation process to separate chemicals. Separation of important gases typically through cryogenic distillation however is highly energy-intensive. For example, U.S. Department of Energy estimates that olefin/paraffin separation consumes approximately 0.12×10^15 Btu of energy per year.
Membrane technology in particular is promising for energy-efficient gas separations due to its inherent advantages such as high efficiency, low energy requirement & linear scale-up. Sholl & Lively estimate that membrane technology can save up to 90% of energy as compared to the thermally-driven distillation process. Compact membrane modules offer operational flexibility, allowing the modules to function as standalone unit or to be retrofitted into existing process unit. In general gas separation membranes can be classified into three categories: (i) organic polymeric membranes (ii) mixed matrix membranes (iii) inorganic membranes
Gas Separation Membranes
Ultrathin ZIF-8 Membranes on Polymer Hollow Fibers
A prototypical ZIF, ZIF-8 has an effective aperture of 0.4 nm, making them perfect for isolating hydrogen (0.28 nm) or propylene (0.4 nm) from propane (0.42 nm). A kinetic uptake measurement showed that ZIF-8 has intrinsic propylene/propane selectivity of 130. Unlike the commercial polymeric membranes, inorganic membranes however is prohibitively expensive with full module cost of $5,000 - $10,000 per sq. meter (~75% of the cost comes from the use of expensive ceramic support btw). Utilization of cheap polymer substrates ($5 - $10 per sq. meter) can make ZIF-8 membrane synthesis economically more attractive. Reducing membrane thickness to sub-100 nm thick significantly increases membrane flux which help to justify high cost of inorganic membranes. We managed to fabricate a sub 1-micron thick ZIF-8 membranes on PVDF & Matrimid hollow fibers showing attractive permeances & separation factor surpassing the commercial requirements.

dsbf
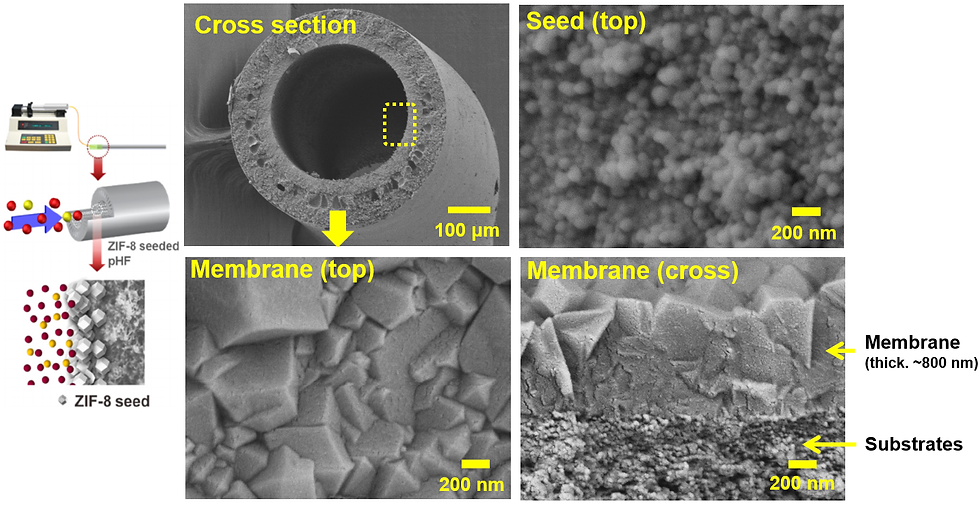
Untitleds

Untitledjkjk

dsbf
1/9
The concept of MMMs is introduced to overcome the limitations of both polymer & inorganic membranes. MMMs are composite membranes comprised of nano/micro-sized particles, usually more selective, homogeneously dispersed in a continuous polymer matrix. MMMs merge desirable properties from both phases: high permeability & selectivity of inorganic fillers (molecular sieve materials) & cost & processing convenience of polymer. MMM synthesis via conventional physical blending methods often lead to unsatisfactory microstructures (e.g., interfacial structures & filler dispersion) resulting in moderate selectivity improvement. While fabrication of flat sheet MMM is relatively straightforward, transitioning to hollow fiber MMMs is more challenging because of the complicated variables of hollow fiber-spinning processes.Recently, we presented a new scalable MMM fabrication protocol which is based on polymer modification strategy, namely PMMOF. PMMOF enables in-situ formation of ZIF-8 and hybrid ZIF fillers inside a submicron thick (750 nm) selective skin layer. It is worthy of mentioning our PMMOF MMMs have the thinnest skin layer and one of the best separation performances among the reported MMMs.
In-situ Mixed Matrix Membrane for Gas Separations
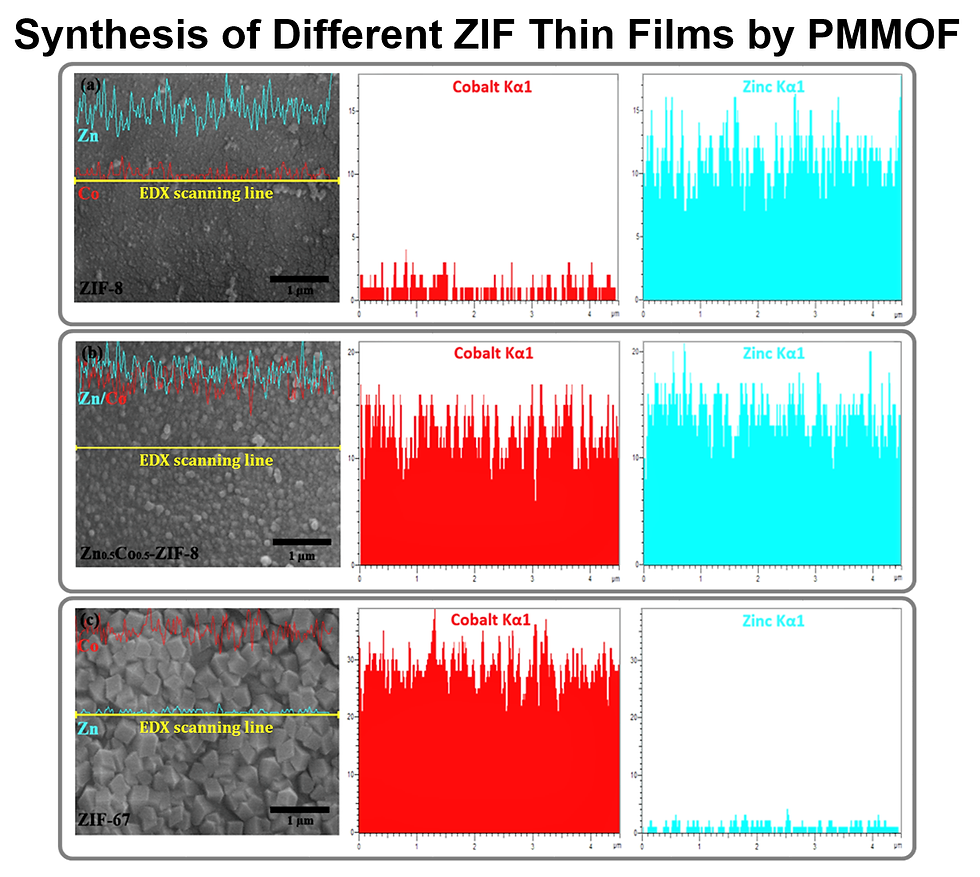
sd
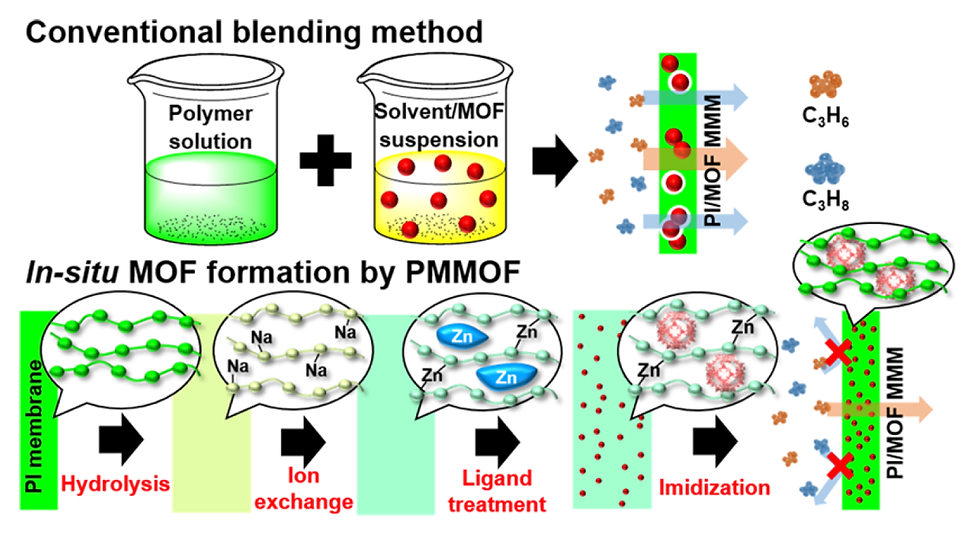
sdd
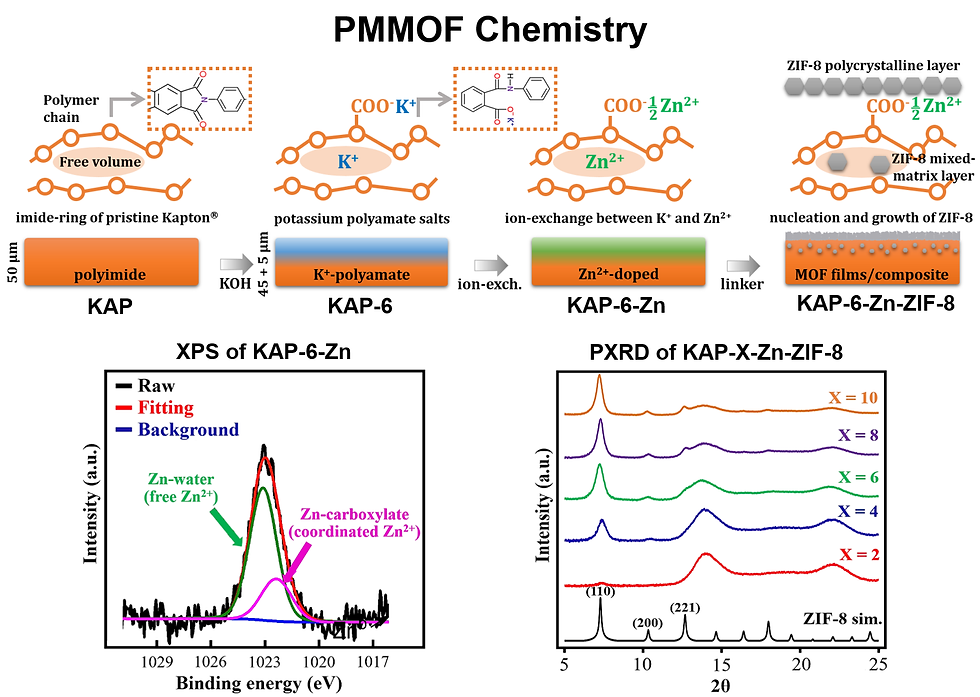
jjd
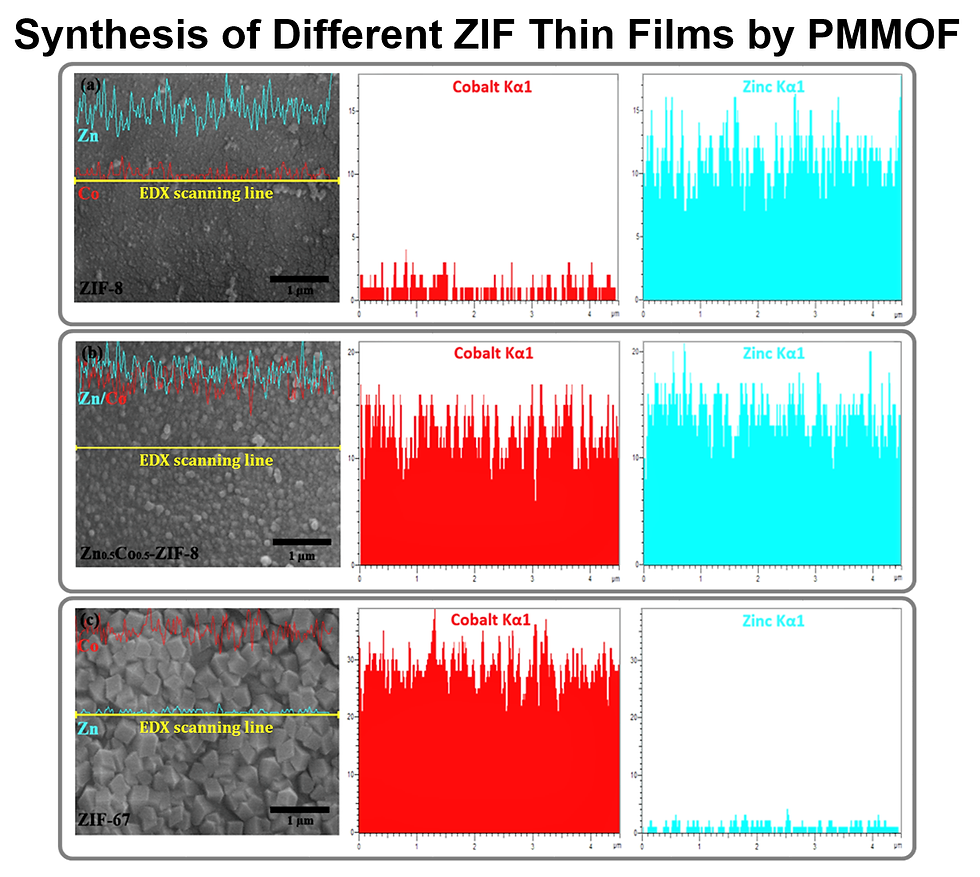
sd
1/4
One of the limitation of ZIFs being crystalline materials is their apertures are discreet. For instance, ZIF-8 with effective aperture of 0.4 nm is highly efficient in separating propylene from propane. Their separation performances, however, is not that great for other gases. The transport properties of ZIFs can be tailored to target a specific application by incorporating secondary metal (e.g., Zn, Co, etc.) or linker (mIm, eIm, Ica, etc.) into the parent ZIF frameworks by de novo method. Labile nature of coordination chemistry of ZIFs/MOFs enables the secondary metal/linker to be incorporated via post-synthetic modification. We managed to synthesize ZnCo mixed-metal ZIF & ZIF-7-8 crystals & membranes for propylene/propane separations. We are currently working on a project to synthesize mixed-linker ZIF powders & membranes to target other gas mixtures.
Hybrid ZIF Adsorbent & Membranes
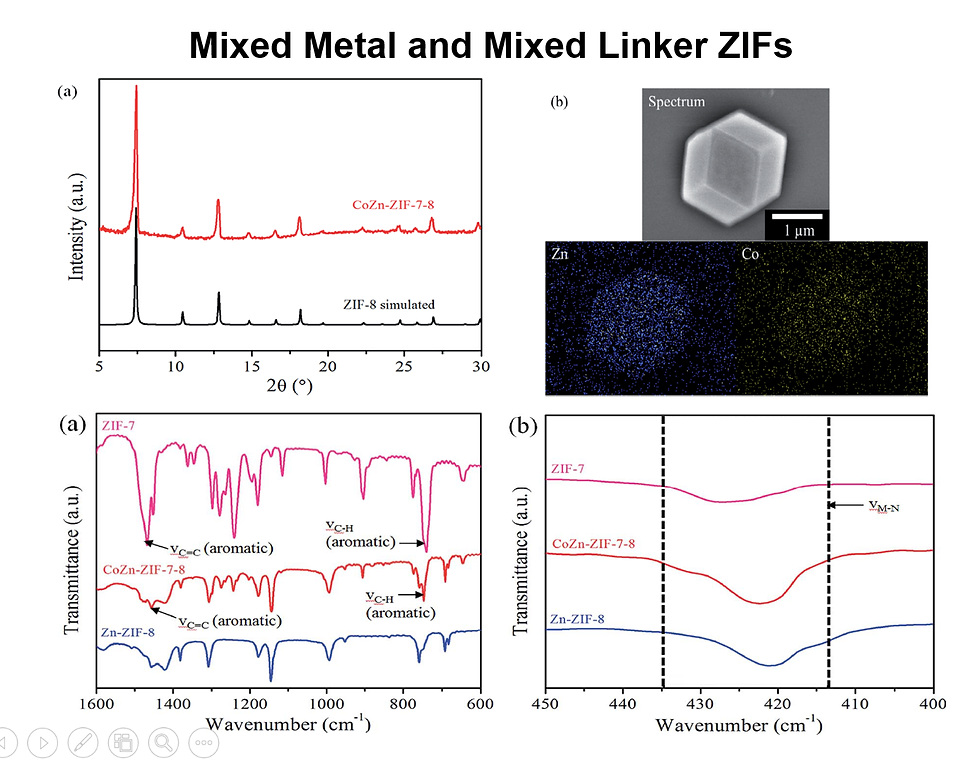
4w

3w

2w
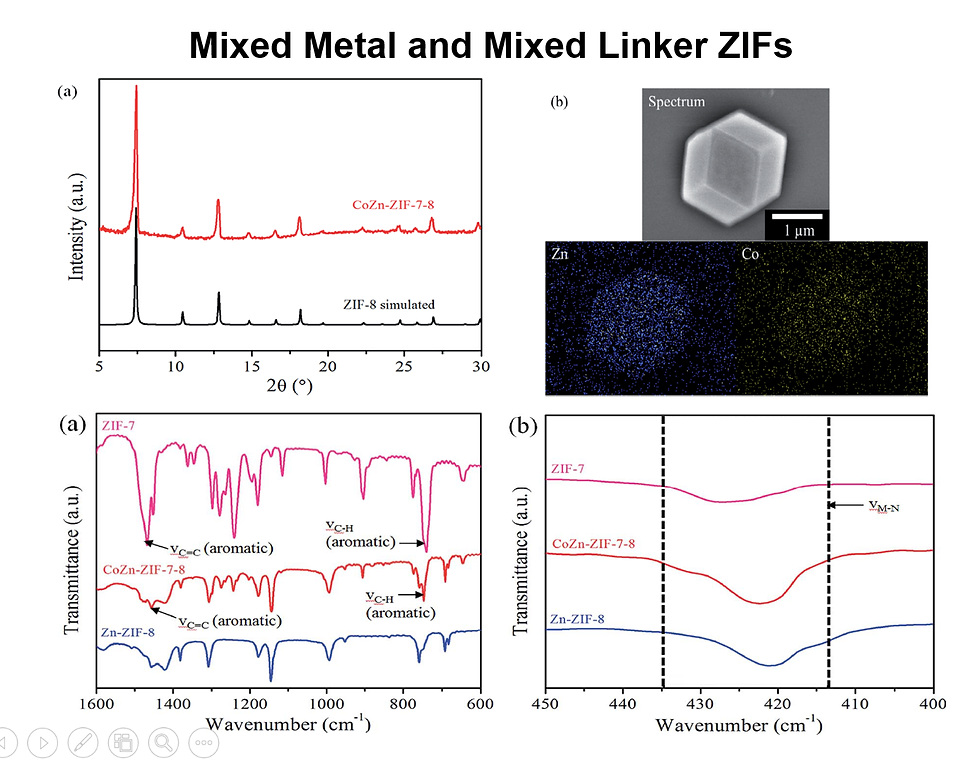
4w
1/4
In addition to material synthesis, we also have expertise in Aspen Plus process simulation software. Our current Aspen Plus industry project is a simulation study of biomass or solid waste combustion/incinerator processes with an hourly capacity of 1 - 3 metric tonne for our client in Selangor

Biomass Incineration Process Aspen Plus
bottom of page